Sostenibilità e riciclaggio: caccia all’ultimo elemento
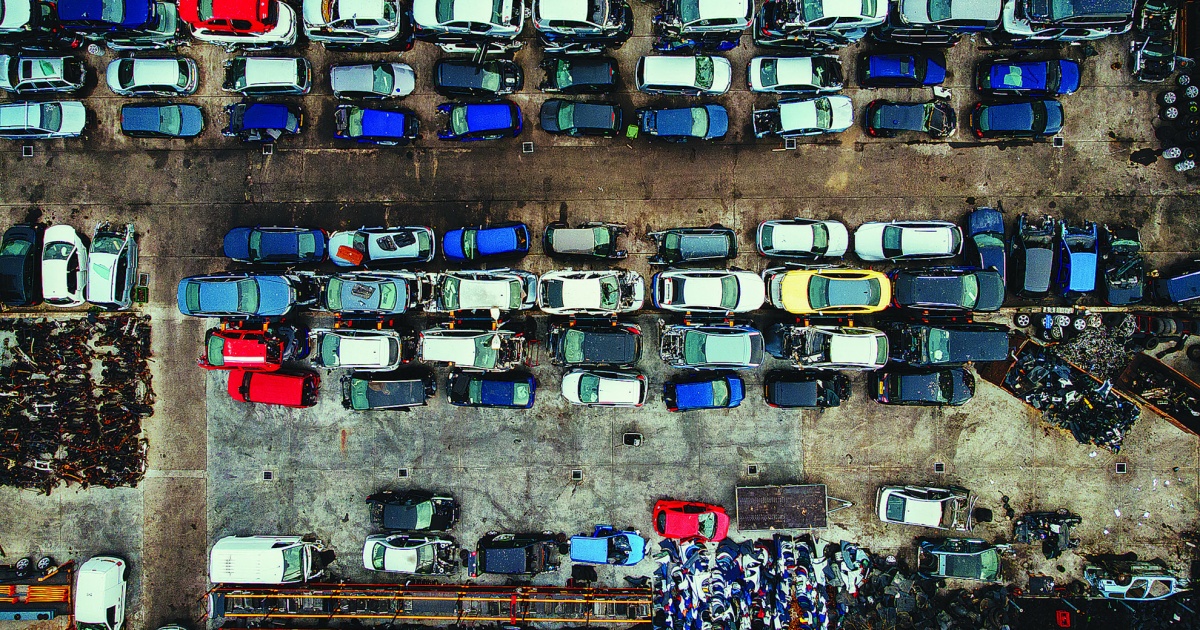
Scarti… preziosi quelli dell’automobile. Una volta arrivata al termine del ciclo di vita, oggi delle vetture non viene infatti buttato via quasi nulla
Di AS
Pubblichiamo un contributo apparso su Ticino7, allegato a laRegione
Gran parte dei componenti e dei materiali costitutivi provenienti da una vettura di serie è avviata in specifici processi di riutilizzo o di recupero, in modo da soddisfare sia le esigenze ambientali sia quelle puramente economiche. Il componente oggi al centro dell’attenzione è indubbiamente rappresentato dalle batterie al litio, cuore della crescente elettrificazione della mobilità su ruota – ne parliamo approfonditamente in altri contributi presenti in questa pubblicazione –, ma in generale la rincorsa al recupero dei materiali è un tema centrale; le materie prime sono comunque costose e il loro approvvigionamento ‘ex novo’ lo è oggi ancora di più rispetto al riutilizzo delle materie di base. Il riciclo è tra l’altro da tempo previsto dalla stessa legislazione europea, che dal 2015 richiede l’obbligo per i costruttori in grande serie di immettere sul mercato modelli che permettano la possibilità di recuperare fino al 95% della loro massa complessiva, di cui il 10% inteso sotto forma di recupero energetico. Non tutto ritorna a bordo delle nuove vetture, tuttavia: attualmente circa un quarto dei materiali viene riutilizzato direttamente in forma di componente automobilistico, mentre la maggior parte delle rimanenze trova applicazione in altri cicli produttivi.
Chi ha una vettura di recente costruzione lo sa: le plastiche sono sempre più abbondanti sull’automobile, arrivando a costituire un buon 50% del volume del mezzo completo. La plastica si trova dappertutto: elementi di arredo interni, pannelli delle portiere, attorno ai montanti, all’interno dei paraurti, nel vano motore e altro ancora. I polimeri plastici si sono evoluti continuativamente, specie negli ultimi due decenni, offrendo indubbi vantaggi: sono resistenti e hanno un’elevata tolleranza al calore, possono essere stampati direttamente a tutto vantaggio della versatilità e del contenimento dei costi di produzione e sono realizzabili rapidamente, entrando in produzione molto più velocemente di altri materiali. La plastica è inoltre leggera e permette di ridurre la massa complessiva di un veicolo, potendo fare spazio per ulteriori tecnologie e componenti di bordo.
Oggigiorno, l’industria automobilistica è così divenuta il terzo settore di consumo di polimeri dopo l’imballaggio e l’edilizia; vengono mediamente impiegate quasi quaranta tipologie di materie plastiche di base, con oltre il 70% delle componenti derivato da quattro elementi principali: polipropilene, poliuretano, poliammidi e PVC. Ogni tipologia di plastica va recuperata in maniera diversa, con alcune di queste che devono essere prima frantumate per poi essere avviate al riciclo per dar vita a nuovi oggetti ed elementi nei campi di applicazione più vasti. Moquette e tappetini vengono ad esempio trasformati in materiale per creare nuove strade o riparare quelle già esistenti, mentre gran parte dei tessuti (sedili, rivestimenti) è ormai di tipo sintetico: resina termoplastica che viene trattata e trasformata in filato mediante un processo raffinato, dando origine a materiali qualitativamente di ottimo livello.
© Shutterstock
Metalli, pneumatici e vetro
Non meno importanti sono i metalli, costituendo il 70-75% del peso di un’automobile. Sono presenti in diverse tipologie, con in testa acciaio e alluminio che possono essere recuperati praticamente al 100% e sfruttati pressoché all’infinito. Il recupero del primo che richiede il 60-75% di energia in meno rispetto alla produzione primaria, mentre la rifusione della lega leggera recuperata dalla frazione di metallo non ferroso impiega solo il 5% di energia rispetto alla produzione a partire dalla bauxite.
Altri metalli meno noti, ma presenti a bordo, sono in ampia misura il rame, il neodimio che trova utilizzo nella produzione di componenti magnetici di microfoni e auricolari, nonché naturalmente l’oro: secondo alcune stime, nel 2015 sulle auto in circolazione nell’Unione Europea si potevano contare ben 400 tonnellate di questo prezioso materiale impiegate in diversi elementi, principalmente connettori elettrici e circuiteria elettronica. Le fasi principali del processo di riciclo di queste materie di base partono dalla selezione delle distinte tipologie di metallo, cui seguono la rispettiva lavorazione e rifusione in lingotti. Questi ultimi sono laminati divenendo lamiere su bobina negli spessori e misure più disparati.
Il riciclo degli pneumatici a fine vita (PFU) permette ormai di ricavare pressoché il 100% dei materiali di base, di cui circa il 70% in materia riutilizzabile e il restante 30% sotto forma di energia di recupero come combustibile per alimentare impianti industriali, principalmente cementifici. Il PFU è infatti caratterizzato da un potere calorifico pari a quello del carbone, ma con emissioni nettamente inferiori. Industrialmente, gli pneumatici usati vengono ridotti e triturati scindendone i componenti in tre grandi famiglie, vale a dire granulato di gomma – materiale quest’ultimo successivamente frantumato in particelle ridotte fino a ottenerne una sorta di sabbia (polverino) -, acciaio e fibre tessili.
Con la gomma riciclata, in particolare, si realizzano svariati prodotti ecosostenibili, che trovano applicazione in settori anche molto diversi tra loro: prodotti per l’edilizia come isolanti acustici e antivibranti, componenti per lo sport come basi per parchi giochi, campi da calcio, pavimentazioni sportive polivalenti, prodotti per il benessere animale. Vengono inoltre impiegati nel settore delle strade e infrastrutture, dove – accanto agli asfalti “modificati” silenziosi e duraturi – sono impiegati per piste ciclabili, arredi urbani ed elementi per sicurezza stradale. Infine, queste materie riciclate trovano applicazione nel panorama dei prodotti di design e nell’oggettistica sfruttando nuove miscele che combinano gomma riciclata e materiali termoplastici. L’industria degli pneumatici sta al contempo espandendo i propri programmi di conversione verso l’utilizzo crescente di materie rinnovabili in luogo di quelle convenzionali.
Le componenti vetrose non presentano particolari problematiche di riciclo: parabrezza, lunotto e cristalli laterali sono inviati nei centri di recupero del vetro, materiale riciclabile al 100%. Vi sono poi tutti i liquidi di bordo, a seguire procedure specifiche per tipologia e riutilizzo; vengono separati e trattati carburanti, liquido di raffreddamento, olio degli impianti frenanti e lubrificanti esausti del motore, che purificati sono riutilizzati per nuovi oli oppure impiegati come combustibile in impianti industriali.
© Shutterstock
Piccole bombe ecologiche
Capitolo speciale lo merita lo smaltimento delle batterie, sia quelle convenzionali cui è affidata l’alimentazione dei servizi di bordo, sia quelle più specifiche ideate per la trazione sui modelli ibridi, ibridi ricaricabili ed elettrici. Le batterie convenzionali contengono sostanze altamente nocive per l’ambiente; tra le tante, metalli pesanti come piombo, rame, cromo, cadmio, zinco e mercurio, oltre agli acidi con particolare riferimento a quello solforico. I moderni trattamenti di riciclo consentono di raggiungere una quota di recupero pari a circa il 90-95%, potendo riutilizzare quasi la metà dei componenti per nuove finalità: per prima la realizzazione di nuovi accumulatori, mentre altri elementi come il piombo trovano applicazione anche in settori diversi tra cui chimica ed edilizia.
Il riciclo delle batterie delle auto elettriche rappresenta invece una sorta di sfida nella sfida per ottimizzare l’utilizzo delle risorse e promuovere un’economia circolare. La tecnologia oggi garantisce un adeguato e sicuro smaltimento delle batterie, seppur ancora costoso; d’altro canto il mercato globale dell’accumulo di energia è in grande crescita, con previsioni che indicano una capacità installata in espansione di ben 35 volte entro il 2030: se nel 2020 la domanda globale di batterie è stata di 282 GWh, ci si aspetta che entro il 2030 questa cifra salga a 3’500 GWh. Con il mercato delle auto elettriche a determinare una spinta senza precedenti verso un utilizzo su larga scala delle batterie, perlopiù della tipologia agli ioni di litio. La loro vita utile ha però un limite, che attualmente si aggira sugli 8-10 anni, al raggiungimento del quale vanno sostituite. Entro il 2030 in Europa servirà dunque una capacità di riciclo pari a 420mila tonnellate di materiale per batterie ogni anno (fonte: Fraunhofer ISI, 2023).
Quando la batteria al litio esaurisce il proprio compito a bordo dell’auto, restano due strade percorribili per garantire la sostenibilità del loro processo di vita: l’impiego ulteriore come fonte di accumulo di energia elettrica, elemento strategico e sempre più decisivo per raggiungere gli obiettivi di decarbonizzazione e di transizione energetica (“second-life battery”), infine lo smaltimento in appositi impianti. Nel primo caso, la batteria al litio non più adeguata ad alimentare efficacemente un veicolo elettrico conserva tuttavia una capacità residua di accumulo che si aggira intorno al 75%, rivelandosi sufficiente per diventare un sistema di accumulo di energia per impianti fotovoltaici domestici, per immagazzinare l’energia elettrica prodotta in eccesso durante il giorno, per fronteggiare picchi di domanda. A livello sia domestico sia industriale, dove in quest’ultimo scenario numerosi elementi vengono collegati a formare veri e propri impianti di stoccaggio e riserva di energia elettrica da rimettere in circolo in base alla necessità.
© Shutterstock
Virtuosismi ed economia circolare
Al termine effettivo del ciclo di vita di questo genere di accumulatore “moderno” serve infine affrontare il suo riciclo finale. Gli attuali costi di smaltimento sono elevati, stimati in circa 4-4,5 euro in zona Europa presso i centri specializzati in queste operazioni, ma in svariati Paesi dell’Eurozona è già in corso di forte espansione lo sviluppo di sistemi di smaltimento più efficaci e automatizzati, attraverso l’iniziativa di consorzi e aziende private.
Evoluzione che mette in moto diversi scenari virtuosi: abbattimento drastico della spesa di riciclo, sviluppo dell’economia circolare correlata a questa attività, recupero e stoccaggio di significative quantità di materie rare di base (litio in primo piano, ma pure nichel, cobalto, manganese) per il successivo riutilizzo in nuovi accumulatori. Aprendo così le porte alla maggior indipendenza nei confronti del reperimento in natura e della fornitura di questi materiali rari, costosi e preziosi, tuttavia necessari al funzionamento di questo genere di accumulatore. Tecnicamente, il riciclo finale della batteria al litio esausta prevede smontaggio e suddivisione dei singoli componenti (moduli e celle), frantumazione meccanica e recupero di metalli rari oltre a ferro, rame, alluminio attraverso diverse lavorazioni mediante pirometallurgia e/o idrometallurgia. La prima liquefacendo alcuni dei metalli con litio e alluminio come residui, la seconda tesa a estrarre e isolare in purezza ulteriori metalli attraverso complessi processi chimici.
© europarl.europa.eu
© Shutterstock